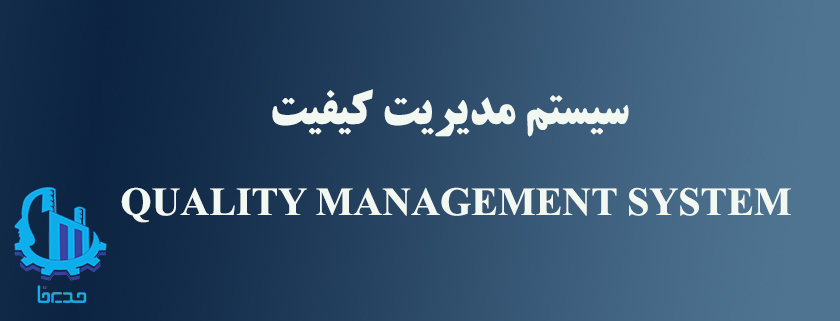
General quality management system
The quality management system helps to coordinate and guide the activities of the organization to meet the customer’s needs and also to improve the efficiency continuously. A quality management system is defined as a formal system that documents the steps and responsibilities related to the achievement of quality policies and objectives.
The ISO 9001 standard is an international standard that specifies the requirements for quality management systems and is also the most prominent approach in quality management systems.
Objectives of the quality management system
While some use the term quality management system to describe the ISO9001 standard or a group of documents detailing the quality management system, it actually refers to the entire system. The documents are provided only to describe the system.
- Improve processes
- waste reduction
- reduction in costs
- Facilitate and identify educational opportunities
- Reducing employee engagement
- Orientation at the organization level
Advantages of quality management systems
The implementation of a quality management system affects all aspects of the organization’s performance. Also, its benefits include the following:
Responding to customer needs, which helps stimulate confidence in the organization and in turn leads to more customers, more sales, and more repeat business.
Meeting the needs of the organization, which guarantees the space for expansion, growth and profitability by complying with the regulations and providing the most affordable and cost-effective products and services.
These benefits provide other services, including helping to communicate readiness for continuous production, preventing mistakes, reducing costs, ensuring processes are defined and controlled, and continuous improvement.
Elements and requirements of a quality management system
Each element of QMS helps to achieve the overall goals of meeting the needs of customers and the organization. Quality management systems must meet the unique needs of the organization. However, the common elements of all systems are:
- Quality policy and quality objectives of the organization
- Quality guide
- Procedures, instructions and records
- Data management
- Internal processes
- Customer satisfaction with product quality
- Opportunities for improvement
- Quality analysis
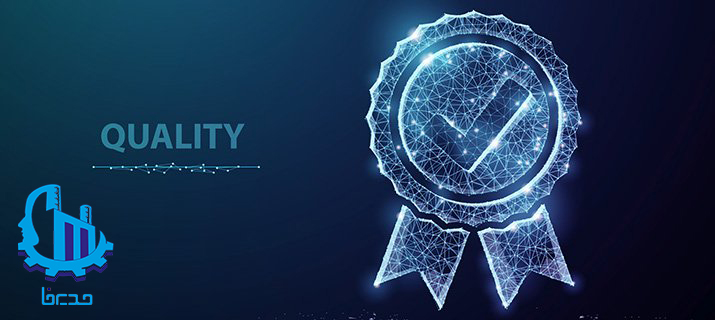
Establishment and implementation of a quality management system
Before creating a system, your organization must identify and manage various connected and cross-functional processes to help ensure customer satisfaction. The QMS design should be influenced by the organization’s goals, needs, and various products and services. This structure is mainly based on the Plan-Do-Check-Act cycle: PDCA is robust and enables continuous improvement for both the product and the quality system. The basic measures to implement the quality system are as follows:
- Plan
- Build
- Establishment
- Control
- Measure
- review
- to improve
Design and construction
The design and construction departments are responsible for developing the system structure, its processes, and programs for implementing effective services. The senior management must supervise this department to meet the needs of the organization and the needs of the customers are the driving force for the development of the systems.
Establishment
Deployment is best delivered by breaking down each process into sub-processes and training employees on documentation, training, training tools and metrics. .
Control and measurement
Control and measurement are two areas for establishing a QMS, which is largely accomplished through routine and regular audits of the quality management system. Its specifications vary from organization to organization depending on the size, potential risk and environmental impacts.
Industrial impact on quality and standardization
The history of quality can trace its roots back centuries, when artisans began to organize themselves into unions called guilds. When the Industrial Revolution arrived, early quality management systems were used as criteria that controlled product and process outcomes. As more people had to work to produce results and production quantities grew, best practices were required to ensure quality results.
History of quality management
Quality became increasingly important during World War II, for example, when bullets made in one country had to work with rifles made in another. The armed forces initially inspected almost every product unit. To simplify the process without compromising safety, the Army used qualitative sampling techniques using Walter Schwartz’s publication of Military Specification Criteria and training courses in statistical process control techniques.
The importance of quality management after the World War
The importance of quality only increased after the war. The Japanese enjoyed a quality revolution, and by fully embracing the arrival of American thinkers such as Joseph M. Joran and W. Edwards Deming, they improved their quality reputation for shaky exports and shifted the focus from inspection to improving all of the organization’s processes through people from whom They used to change. By the 1970s, American industrial sectors such as electronics and automobiles were expanding with Japanese quality competition.
Conclusion
With that said, in simpler terms, a quality management system such as ISO 9001 is a well-defined set of business processes. Together with relevant documentation, it defines your commitment to create products and services according to predefined standards. A good QMS should contain detailed information about the processes and responsibilities in an operational environment.
ISO 9001 quality management system standards are designed to help and ensure an organization meets the needs of customers as well as their stakeholders while complying with regulatory requirements related to their products or services. During the development and implementation of a quality management system, the use of ISO 9001 consultants can be an important advantage.
No views