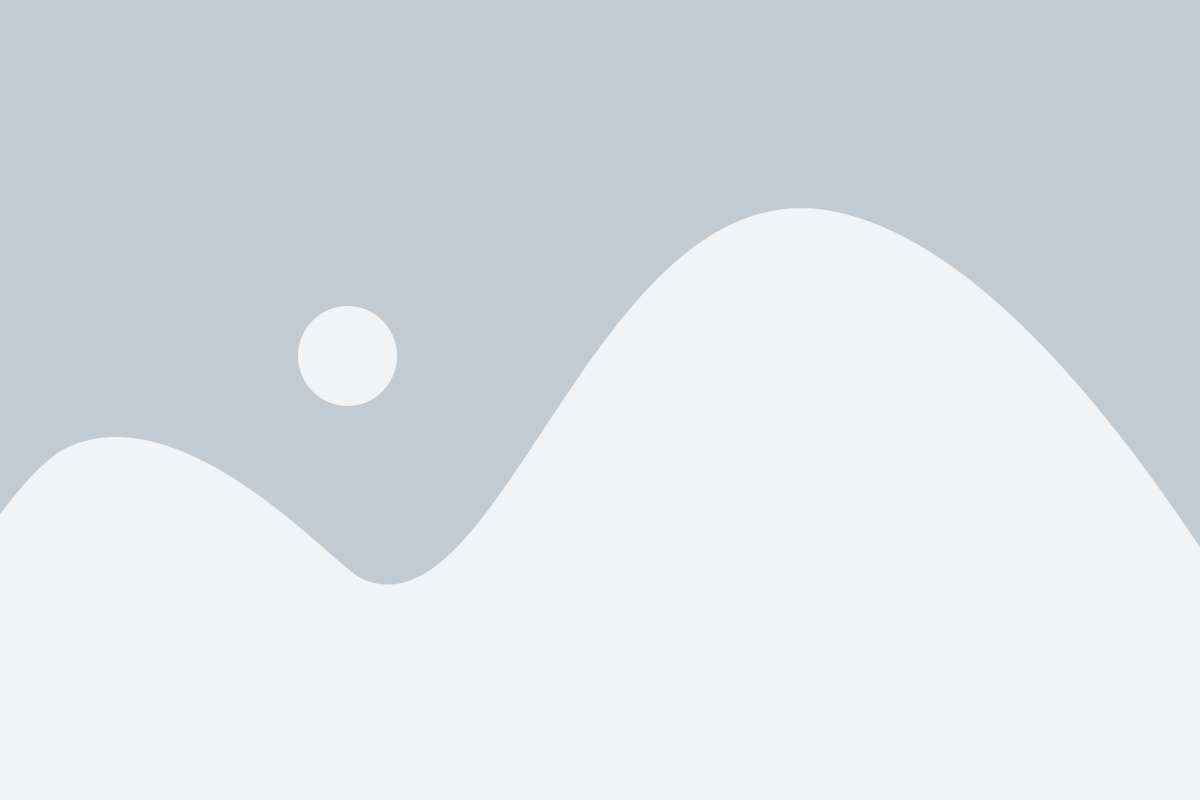
Implementation of ISO 9001 for quality management systems:
ISO 9001 quality management system standards are designed to help and ensure an organization meets the needs of customers as well as their stakeholders while complying with regulatory requirements related to their products or services. During the development and implementation of a quality management system, the use of ISO 9001 consultants can be an important advantage. In the following article, we will describe the steps of ISO 9001 implementation:
ISO 9001 implementation steps:
Step 1 - Formation of the executive team:
The first step in the implementation of ISO 9001 is to create a required team of people who are well aware of the quality management system. A team should be led by a service provider supervisor and a management representative. Before implementing ISO 9001, the management representative is responsible for planning and monitoring the quality management system.
Step 2 - Implementation of the awareness program:
It is very important to inform your employees about the quality management system. Therefore, you should carry out a conscious program in the organization to inform your employees about the importance and purpose of the quality management system. It also includes the benefits it provides to customers and employees, as well as the roles and responsibilities of employees within the system.
Step 3 - Checking the initial situation:
A quality management system must be established with the approval of ISO 9001 standards. Now, this step does not prevent merging, adapting, or adding on to an already implemented quality plan. However, this implementation phase basically compares the existing quality management program (if any) with ISO 9001 standards.
Step 4 - Create a documented implementation:
After comparing the quality management system with ISO 9001 standards, the organization uses a documented plan to resolve any non-compliance. The implementation plan documents the process and makes the organization's quality management system fully compliant with the ISO 9001 standard.

Step 5 - Development of quality management system documentation:
Where inconsistencies are most common when it comes to quality management systems is in the area of documentation. To avoid this non-compliance, the following should be developed.
Documented statements of quality and quality objectives.
Documented processes and records required by the ISO 9001 standard.
Documentation required to ensure effective planning, operation and control of processes.
Step 6 - Document control:
A documentation system should be established to control the documents and documents required as part of the quality management system. The document control system should cover the types of documents used as part of the QMS and control the criteria of the ISO 9001 standard.
Step 7 - Internal quality audit:
To check the effectiveness of the quality management system, it should be checked by the quality assurance or internal audit team. Below are the reasons for conducting internal audits:
To ensure that the quality management system complies with its requirements as well as with the requirements of the ISO 9001 standard.
To ensure that the quality management system is implemented in an effective manner.
For continuous improvement in your quality management system.
Step 8- Review by management:
After the implementation of the quality management system, management reviews should be carried out at scheduled intervals. There is no required frequency, however many organizational managements review at least once a year. This is to check the ongoing effectiveness of the system.
Step 9- Certification and registration:
The official request as a certificate is made by the certification organization after 3-6 months of implementation and stabilization of the ISO 9001 standard. A certification body issues the license only if the quality management system meets the requirements of the ISO 9001 standard. This certificate is valid for 3 years and surveillance audits are conducted during that period.
Step 10 - Continuous improvement:
After obtaining the certificate from the certification organization, the organization should focus on continuing the efficiency and stabilization of the quality management system in order to meet the needs of its customers and increase their satisfaction.
This guide provides a good overview of the steps to take when implementing your ISO 9001 compliant quality management system.
If you are looking for professional support with your implementation, we are more than happy to help. Please contact our experts for a free quote on your project.
Phone number : 88761795-88764867-021
ISO 9001 standard and GMP Both focus on quality assurance, but there is a difference between the two, ISO 9001 is a general business-focused standard that supports effective quality management to an internationally recognized level. in return , GMP (Good Manufacturing Practice) is a specific industry standard that must be met to ensure product safety and efficacy.
No views