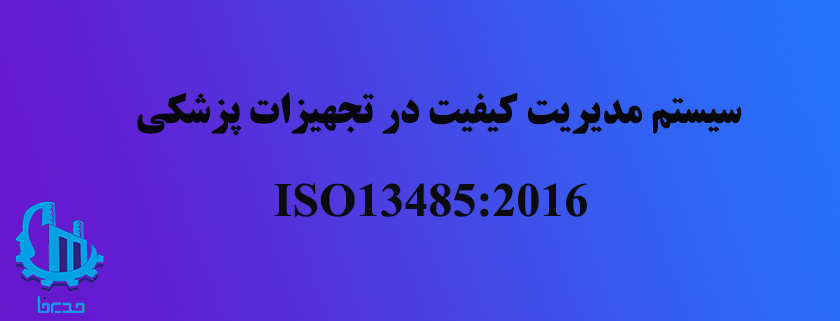
Quality management system standard in medical equipment industry
The ISO 13485 standard is based on the ISO 9001 process model approach and is a management systems standard specifically designed for the manufacture of medical devices and equipment. ISO 13485 was written to support medical device manufacturers in designing quality management systems that establish and maintain the effectiveness of their processes. This is consistent with the design, development, manufacture, installation and delivery of medical devices that are safe for their intended purposes.
Importance of quality management system standard in medical equipment industry
The ISO 13485 standard specifies requirements for a quality management system in which an organization must demonstrate its ability to provide medical equipment and related services that consistently meet customer needs and applicable regulatory requirements. Such organizations can be involved in one or more stages of the life cycle, including design and development, production, storage and distribution, installation or service of a medical device.
The ISO 13485 standard can also be used by suppliers or external parties who provide products, including services related to the quality management system, to such organizations.
The requirements of ISO 13485 standard are applicable to organizations regardless of their size and regardless of their type, with the exception of those expressly stated. Wherever the requirements are for medical devices, the requirements are equally provided for the services related to the organization.
Since you are conducting your own audit process and also have a certification body auditing them, clients themselves do not need to audit your company. That is why the ISO 13485 standard has become a necessity for many companies to compete in the market.
ISO 13485 standard structure
The structure of the ISO 13485 standard is divided into eight parts, as it corresponds to ISO 9001. The first three items are preliminary and the last five items include the requirements of the quality management system. Here are five main points about these things:
Clause 4 of the quality management system
This clause talks about the general requirements of the quality management system as well as the requirements of standard documents. This includes requirements for quality manuals, control documents, and control records, all of which are required documents in a QMS.
Clause 5 Management responsibility
Management responsibility requirements considers the needs of top management in the implementation and maintenance of an effective quality management system. Along with planning for the quality management system, there is a need for top management to continuously review the system to ensure customer satisfaction and improvement.
Clause 6 resource management
The resource management section is short, but it includes the need to control all resources, including human resources, buildings and infrastructure, and the work environment.
Clause 7 product realization
Product requirements deal with all aspects of planning and creating a product or service. This section includes requirements for planning, reviewing product requirements, designing, purchasing, creating the product or service, and controlling the equipment used to monitor and measure the product or service. ISO 9001 allows the requirements in this section to be omitted if this section is not used in the organization (such as an organization that does not design products or services).
Section 8 Measurement, analysis and improvement
The last paragraph contains the requirements to ensure that you can monitor whether your QMS is working well. This includes evaluating customer satisfaction, internal audits, monitoring products and processes, dealing with non-conforming products, and corrective and preventive actions.
These clauses are based on the Plan-Do-Check-Act cycle, which uses these elements to implement change in the organization’s processes in order to drive and sustain improvements in the processes.
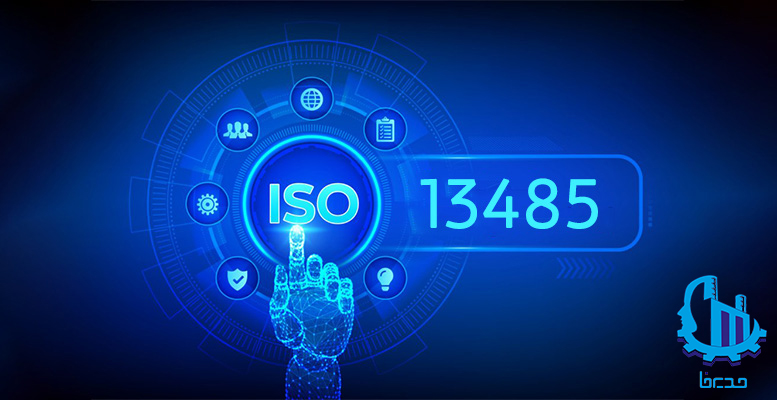
Advantages of implementing the ISO 13485 standard
Considering the wide range of benefits of ISO 13485 standard, it is not possible to express a large number of these benefits. Companies large and small have used this standard to great effect, discovering and securing cost savings and tremendous productivity. Here are just a few of these benefits:
Improving the image and reputation of the organization
When customers see that you are recognized by a certification body, they understand that you have implemented a system that is focused on meeting customer needs and improving them. This improves their confidence that you will deliver what you promise.
Improve customer satisfaction
One of the important principles of the ISO 13485 standard is to focus on improving customer satisfaction by identifying and meeting customer needs and wants. By improving satisfaction, you improve repeat customer business.
Fully integrated processes
Using the ISO 13485 process approach, you look not only at the individual processes in your organization but also at the interaction of those processes. With this, you can more easily find areas to improve and save resources in your organization.
Evidence-based decision making
Ensuring good evidence-based decision making is key to the success of an ISO 13485 standard. By ensuring that your decisions are based on good evidence, you can best target resources to correct problems and improve your organizational efficiency and effectiveness.
Create a culture of continuous improvement
With continuous improvement as the primary output of the quality management system, you can achieve incremental gains in saving time, money, and other resources. By building this culture in your company, you can focus your workforce on improving the process they are directly responsible for.
Personnel participation
Who better to find the best solutions to improve the organization than people working in a process? By focusing our workforce not only on management but also on process improvement, we contribute more to the continuous improvement of the organization’s bottom line.
ISO 13485 guides organizations to improve the quality of their products and services with the ultimate goal of achieving customer satisfaction and adhering to all legal and regulatory requirements.
Achieving the ISO standard requires commitment and measurement of time and resources. By using appropriate procedures, processes and existing documentation, an organization can have a positive reputation in the global markets through improving product quality and customer satisfaction. to have financial possibility.
For a free consultation in the field of medical equipment quality management system, contact the experts of Modirfa.
02188764867 – 02188761795
No views