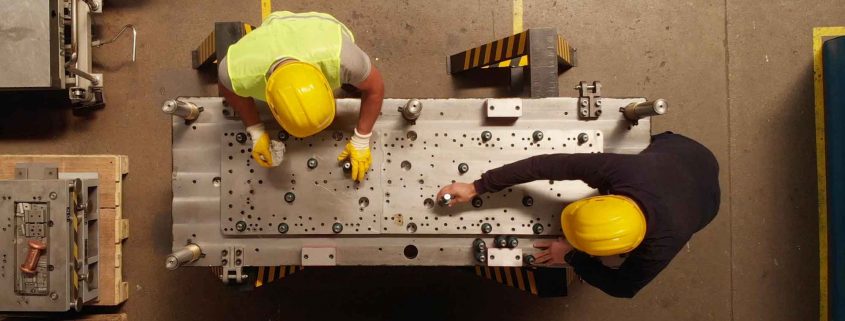
Contact our advisors at Modirfa to get a free consultation on the implementation of the Six Sigma approach.
02188764867-02188761795
process capability
Based on the experiences gained in Noor’s group of consulting engineers, every process in the organization has a potential level called process capability, which most organizations do not operate at this level. This vacuum is caused by some factors (operator, device, environment, etc.).
To facilitate the implementation of six sigma improvement projects by the experienced group of Noor consulting engineers, the first suggestion is to match the actual process capability to the potential process capability. Because this change, however small, due to the non-linear behavior of the processes, causes a significant improvement in the performance of the process and a huge reduction in the quality costs of your processes.
Every product or service provided by the organization has parameters that satisfy the customer’s needs. Each parameter has requirements that are determined by national and legal standards, the customer, the system standard or the provider organization itself.
In case of producing a product or providing a service that does not meet these expectations and needs, it will cost the organization a lot. Each of these parameters is the output of a particular process. The outputs of these processes are not always constant and variable values are obtained due to some errors from the operator, environment, device, execution method, etc.
Process potential
Therefore, as mentioned, the outputs are not equal and it can be said that the outputs have a random distribution. One of the criteria for measuring the ability of the process in compliant production is the process capability criterion (Process Capability) or Cp.
Process capability is a measure of the process’s potential ability to produce a conforming product, which is calculated as follows:
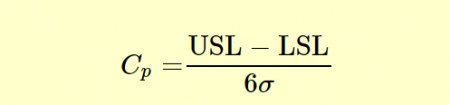
To interpret the above statement, pay attention to the following example:
Suppose the Cp of a process equals 2, this means that the distance between the acceptance limits of your customers is twice the dispersion of the distribution curve of the process outputs, and the mean of your process is free to move within this mean, without your process producing a non-conforming product.
The acceptable value of this criterion for each process is 1.33, which most of the country’s organizations have not reached this value. It is interesting to know that even in this situation, which is considered acceptable, the organization spends 30-40% of their sales cost. They pay for the bad quality of their product.
The actual capability of the process
It is interesting to know that this amount of cost is in exchange for your process to work in its potential state, i.e. the process conforms to the average, but unfortunately, most of the processes of current organizations do not conform to the average and the cost is more than the said cost. impose on their system.
The actual process capability is also calculated as follows:
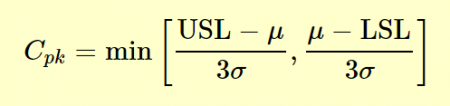
Comparison of the capabilities of potential and actual processes
For a better understanding of the proposed concepts, pay attention to the figure below.
Right column
The first one has a high dispersion in the output
Cases 2 and 3 can be seen that the peak (mode) of the process is not centered on the center (mean). In the first step in the phase of improvement projects, Noor Group of Consulting Engineers is trying to correct these issues.
Left column
All cases have a small scatter, and having a small difference in the mean does not result in inconsistent output.
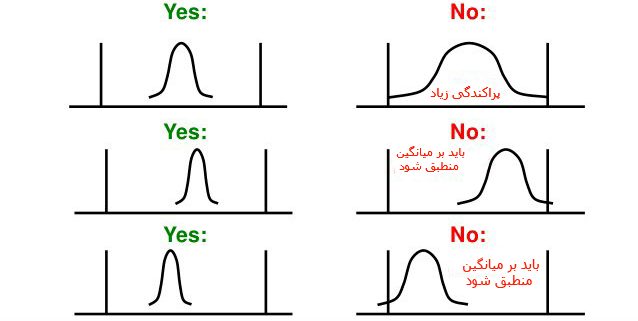
A case study of Noor Consulting Engineers Group
The graphs and output reports of one of the projects carried out by Noor Consulting Engineers Group (modirfa) for one of the suppliers of the automotive industry are as follows.
According to the diagram on the right It is known that the capability of the process in the short-term mode (dashed line) and in the long-term mode (red line) is far from the average, and based on the analysis of the engineering team, it was determined that the costs imposed on the system due to losses in this case It is equal to 50-60% of the sales revenue of that product.
In the graph on the left, with the improvements created, only in the average samples, it can be seen that a smaller amount of products fall outside the requirements (technical specifications) and in this case, 30-40% of the sales revenue of the product is spent on waste. .
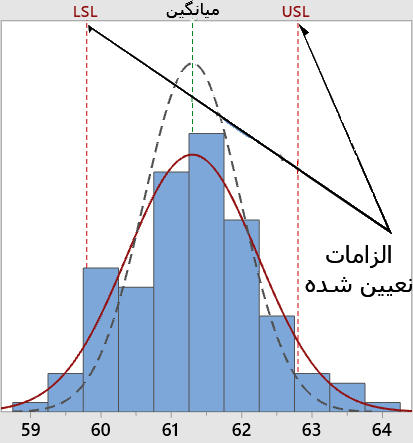

Process capability improvement consulting
In order to implement such improvement projects, which are unique in Iran, it is recommended to use experts in this field as consultants. But note that these types of projects are implemented in a handful of cases in the country. You should consider two important points.
First of all, every consultant does not have the required knowledge in this field and cannot be trusted easily, and if the desired trust is achieved, you will have to pay an exorbitant fee, and finally, there is no guarantee that the output of the project will be the amount of improvement you want.
Considering the aforementioned risks, we are proud to announce that Noor Consulting Engineers Group is ready to implement improvement projects with a six sigma approach at your service, managers and business owners, so that we can create a tremendous and impressive progress in your organization, so that on the way Let us accompany your organization to excellence.
Contact our advisors at Modirfa to get a free consultation on the implementation of the Six Sigma approach.
02188764867-02188761795
Implementation
Only matching the actual process capability to the potential capability leads to a significant leap in reducing the costs of the organization.
Beware of unlicensed and fraudulent organizations.
Be sure that if an organization gives you an ISO certificate without implementing it in your organization and conducting an audit, it must be a fraud.