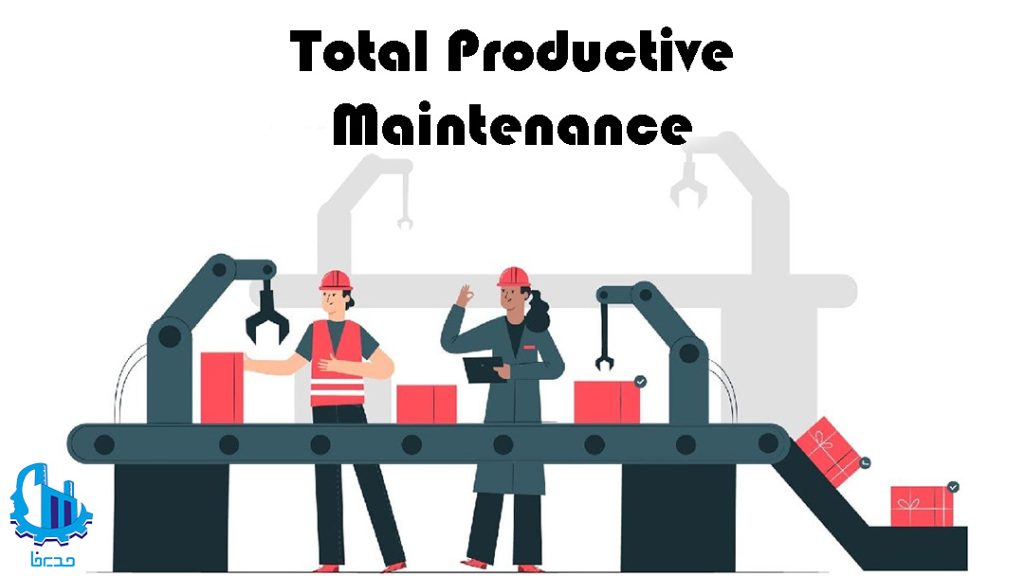
Contact our experts at Modirfa to get free advice on the implementation of comprehensive, efficient maintenance and repairs.
02188764867 – 02188761795
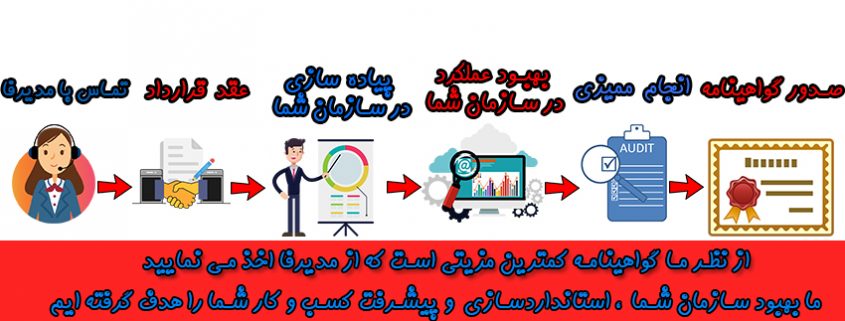
Implementation of comprehensive maintenance and repairs
Certainly, the production equipment of an industrial unit is one of the centers of capital concentration of managers and investors of the organization, and the philosophy of comprehensive maintenance and repairs emphasizes on these valuable assets. Certainly, every CEO is eager to be able to use the maximum production capacity of the organization in order to maximize its production circulation.
But there are many limitations in achieving this goal:
How much will the depreciation of the equipment be?
Is the quality of manufactured products maintained in such a state?
Are the equipment able to respond in such conditions?
In the current situation of the country, considering the existing sanctions and the exorbitant costs of buying parts, one should be more concerned about the condition of the organization's equipment. Even if the managers do not have a goal to achieve the maximum production capacity, they should pay special attention to the maintenance of their equipment, because it can lead to production lagging behind the sales plan or cause high wear and tear of the equipment and finally scrap it. to be equipped.
Comprehensive maintenance and repairs
Comprehensive productive maintenance and repairs is a process for using machinery, equipment, personnel and supporting processes to maintain and improve the integrity of the production and quality system.
According to research by Aberdeen Research in April 2016, the average cost of sleeping per hour in each business is 260 thousand dollars and it seems that this number is increasing every day. So that this amount in 2014 was equal to 164 thousand dollars.
These statistics become alarming when we realize that many manufacturing industries often carry out their production processes through machines and these machines are constantly working.
Simply put, comprehensive productive maintenance and repairs is the process of involving personnel and labor in the maintenance of their equipment so that they use techniques to increase productivity and maintenance.
In fact, comprehensive productive maintenance is focused on using the entire production capacity for a quality product, which means:
- Not sleeping the production line
- Absence of stops and slow working of devices
- No non-conforming product
- Non-occurrence of accidents
Since the goal of comprehensive maintenance and repair is to improve efficiency by reducing production line downtime, implementing a comprehensive maintenance and repair program can have a dramatic effect on overall equipment effectiveness (OEE). be
In order to achieve such a goal, there should always be a background regarding preventive maintenance and repairs in the back of the mind of the organization's personnel.
Basics of comprehensive maintenance and repairs
In the late 1960s and early 1970s, one of the Japanese engineers named Seiichi Nakajima tried to provide the initial definition of comprehensive maintenance and repairs, and then DENSO, which supplied Toyota parts, expanded this model.
This model implies the foundation of the decoration system and 8 pillars:
5S grooming system: In this model, the first step to implement effective comprehensive maintenance and repairs is the establishment of the 5S grooming system, without which the model becomes unworkable, because all the foundations of comprehensive maintenance and repairs are based on this foundation.
Autonomous note: This means making sure that operators are trained enough to perform routine maintenance on their own.
Continuous improvement: Creating small and active teams to continuously improve equipment efficiency.
Planned maintenance and repairs: Studying indicators such as failure rates and failure dates, etc., and creating a plan to prevent failures by defining specific tasks for maintenance and repair technical team members.
Quality system: All efforts for comprehensive maintenance and repairs are made to maintain and improve quality, so without the presence of a quality management system, the effectiveness of the comprehensive maintenance and repairs process is questioned.
Primary equipment management: It includes receiving scientific knowledge and general understanding of equipment to improve equipment design, which can help the supplier to improve or establish new equipment, which can be designed according to the wishes of production experts.
Education : A lack of equipment knowledge can derail a comprehensive, productive maintenance program. Accordingly, operators should learn how to work with the equipment and the skills required for working with the equipment.
Safety, health and environment: Maintaining a safe working environment means that personnel can perform their duties in a risk-free environment.
Effective and comprehensive maintenance and repairs of the office: A good comprehensive productive maintenance program is good as long as all the members of the process are working well. Total production maintenance must go beyond the factory level by addressing and eliminating areas of waste in administrative functions.
Modirfa services in the field of maintenance and comprehensive repairs
Based on the above-mentioned concepts, the Light Management Consultants Group (Modirfa) implements comprehensive and productive maintenance and repairs in 9 phases:
In this phase, along with the establishment of the grooming system, necessary trainings are provided regarding the implementation of the system.
Step 1 - Eliminate clutter in the work space
Step 2 - Determine the location of each equipment
Step 3 - Cleaning the work environment and maintaining cleanliness
Step 4 - Standardization of the work process
Step 5 - Maintaining the status quo and building culture
Conducting training classes to hand over Conditional Maintenance to production line operators and prepare appropriate instructions.
Creating technical teams and providing the necessary training to create continuous improvement by defining appropriate indicators for processes and analyzing the maintenance and repair process and continuous monitoring of the process.
Step 1 - Create a net process data collection system
Step 2 - Collecting data related to equipment failure
Step 3 – Data analysis
Step 4 - Calculate the OEE of the equipment
Step 5 - Analysis and rooting of failures
Step 6 - Preparation of preventive note programs and revision of self-directed note instructions
Along with the implementation of this phase, necessary trainings are provided for the implementation of this step.
Proper definition of quality management system based on ISO 9001
Defining the requirements for each equipment by the workforce and the technical team to improve the equipment or purchase the equipment based on the specified requirements.
This phase may be ignored during the implementation of the project according to the conditions and management's opinion. But the necessary training is provided.
Providing necessary training on how to work with production equipment and preparing required work instructions
Step 1 - Identify the safety risks in the process
Step 2 – Risk assessment
Step 3 - Definition of necessary measures to reduce risk
Step 4 - Implementation of actions
Step 5 - Review work instructions to maintain safety
Establishment of grooming system in the administrative and headquarters environment of the organization
Finally, with the establishment of this process in the organization, the group of management consultants will be at the service of the organization in support, analysis and revision of the system deployed in the organization.
TPM deployment
If you have not defined the appropriate process for handling the equipment and infrastructure of your organization or the current process does not have the necessary effectiveness, we are with you to improve the maintenance and repair processes and establish an efficient and comprehensive system.
Beware of unlicensed and fraudulent organizations.
Be sure that if an organization gives you an ISO certificate without implementing it in your organization and conducting an audit, it must be a fraud.